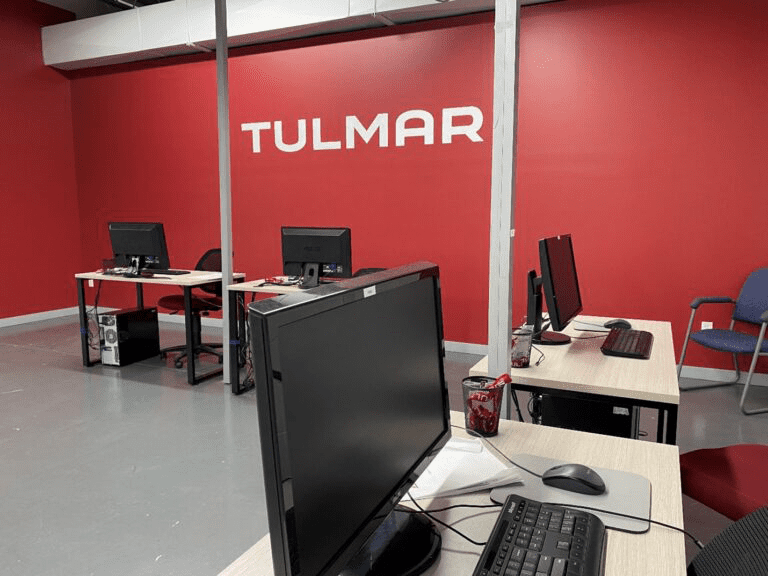
This week marks an anniversary of sorts at Tulmar.
One year ago, a group of our operations managers approached the Senior Leadership Team with a bold idea to completely upend the manufacturing floor of our main plant in Hawkesbury Ontario.
Intuitively we knew this made sense. The natural flow of raw material, work in process and finished goods was awkward.
Good data certainly supports intuition, and these operations managers had their “powder dry” so to speak.
Because of the nature of our business, we track many details of every job that goes through our plant. With this data, our innovative managers did their own time and motion study. They literally walked around the plant, digital pedometer in hand, and measured the footsteps of a wide sample of jobs. With this data, they re-configured our equipment, warehouses, inspection station and testing labs to come up with a proposal to improve our plant.
They were bold indeed!
Here is what they proposed:
- We can save millions of steps per year for our employees by removing non-value-added movement
- We can free up 10% of the plant’s floor space to support our company’s revenue growth targets
- Health and Safety is improved by decreasing raw material movement
- Create a digital hub of PC workstations for production employees to do online training, access their digital payroll records and access our company website and intranet
- “5S” the plant and remove clutter
- Improve inventory turns
- Create a single customer engagement area that showcases our products and services
- Add more collaboration spaces in the facility
- Create a single locker room for production employees to leave their personal belongings as they enter the plant
The price tag for this work was not insignificant, but our intuitive managers had an ROI of 9 months, a plan to do the bulk of the work over our annual summer shut down and a commitment that we would not miss any production targets.
The ROI was impressive, and the team’s confidence was evident with the project plan they presented at the “Improve” tollgate review. They had followed the DMAIC process through this and used data to guide decisions.
July was an incredibly busy month for us as the bulk of the work was done through our annual summer shut down. Summer heat and supply chain shortages didn’t stand in the way of this dedicated group of leaders. We were back in business after the August long weekend and had an entirely new plant floor layout!
As we approach the one-year anniversary, hindsight has proven their thesis correct. The productivity was achieved, we are in the Sustain phase of a plant wide 5S process and we created the unique spaces for our clients and employees.
For me, I took away a few things:
- We have an incredibly committed and talented group of leaders who can make bold assertions and deliver
- Data Driven Decision Making supports bold objectives
- Those closest to the customer or employees can drive the most impactful solutions.
Our website is constantly being updated as we add more unique products to our offering. Check out what we have accomplished and keep an eye in the near future for more announcements at www.tulmar.com.
By Patrick Tallon, President
Tulmar Safety Systems – January 11th, 2022